Respiratory Protection
RESPIRATORY PROTECTION
Just breathe.
Respiratory Protective Equipment (RPE) are included in Personal Protective Equipment (PPE), which are dedicated to protect against life threatening situations or hazards that may cause serious and irreversible health damage, the results of which a worker is unable to foresee quickly enough.
Solid and liquid particles, including nanoparticles, i.e. dusts, fumes, mists, fibers, radioactive particulates as well as vapours, gases and micro-organisms encountered in workplace’s atmospheres can cause significant hazards to health or, in extreme cases, can lead to death. The way in which these hazards occur is by the inhalation of harmful concentration levels of hazardous substances. Moreover, work activities may be carried out in confined spaces or areas where the workers breathing the atmosphere, in some cases even momentarily, with oxygen deficiency (less than 19% by volume), or when concentration of toxic substances are at dangerous levels, or with combination of both.
Health and occupational safety rules require prevention against exposure of employees and others to hazardous substances at work in order to protect their health, safety and wellbeing. Employers must carry out risk assessments and act on them by taking appropriate action. When prevention activities such as collective protection, e.g. elimination or substitution of hazardous material or a change in the process, engineering controls (monitoring of working atmosphere, revised work practices, equipment change, administrative controls) are not available or is not practicable, relevant control measures should be provided in order to prevent hazardous substances from entering the atmosphere. Direct control measures at the source of contamination should always be preferred in order to protect everyone in the workplace, whereas respiratory protection equipment (RPE) only prevents exposure to a single person. However, if applied control measures at the source are not efficient or are inadequate or not possible, then suitable respiratory protection equipment may/will be needed. An example of such a dangerous situation are maintenance activities (e.g. tank cleaning, sludge removal, freezer room repairs), due to the possibility of a sudden release of highly concentrated chemical substances (e.g. organic solvent vapors, trapped process inorganic gases, refrigerant vapors).
There are two general types of respiratory protective equipment (RPE), based on the principle by which protection is provided to the user.
The two types are the following:
Respirators are designed to filter out or clean contaminated air from the workplace atmosphere before it is inhaled by the respirator wearer. Respirators are not designed to be used in atmospheres with oxygen deficiency (concentration of oxygen is below 19%) or where the concentration of unknown contaminants has not been evaluated.
Breathing apparatuses deliver breathable air from an independent source (compressed air vessels, compressed line) to the user. Breathing apparatuses are designed to use in atmosphere with oxygen deficiency (concentration of oxygen is below 19%).
It is of key importance that any RPE that is provided to the workers meet the basic requirements.
Moreover, there is a specific group of RPEs, the so-called rescue equipment, with a limited time of protective performance which allows the user to leave the contaminated area in a very short time. It is not applied for constant activities but is merely equipment for workers to use in rooms or buildings where there is a real risk of sudden emergency.
Both types of RPEs are available with a range of different face pieces, i.e.:
- Tight-fitting face pieces (filtering face pieces, half and full-face masks) that rely on a good fit - seal between the mask and the wearer’s face.
- Loose-fitting face pieces (hoods, helmets) rely on enough air being provided to prevent the contaminant leaking into the face piece as the wearer breathes and moves about. They are used only with powered respirators or with suitable breathing apparatuses.
Respirators
Filter out contamination from the air in the workplace before it is inhaled by the user:
Filtering respirators:
- Filtering face pieces.
- Half mask with filter(s).
- Full-face mask with filter(s).
Powered/assisted respirators:
- Powered hoods and helmets with filter(s).
- Powered-assisted half mask with filter(s).
- Powered assisted full-face mask with filter(s).
Breathing apparatuses
Compressed airline breathing apparatuses:
- Constant flow with any type of face piece.
- Negative demand half or full-face mask.
- Positive demand half or full-face mask.
Indented line Self-contained breathing apparatuses:
- Open-circuit negative demand full-face mask.
- Open circuit positive demand full-face mask.
- Closed-circuit full-face mask demand.
Filtering Devices
Filtering face pieces: these face pieces are often called “disposable respirators”. They either entirely or substantially consist of filter material. They should conform to the EN 149:2001 standard and are classified as FFP1, FFP2 and FFP3 in order of increasing filtration efficiency. There are two types of these respirators i.e. intended to be used for a maximum of a single shift (marked with the letters NR – not reusable), and intended to be used for more than a single shift (marked with the letter R – reusable). The respirators may incorporate inhalation and exhalation valves or exhalation valve(s) only, or have no valves. Where the filtering face piece has no valves, both inhaled and exhaled dangerous substances can pass through the filter material.
There are also valved filtering half masks to protect against gases or vapours and particles. These devices are “disposable” respirators essentially for use against gases and vapours, but with optional protection against particles. Any gas/vapour filters form an inseparable part of the device; any particle filters maybe integral or separable. Complete devices should conform with the EN 405:2001+A1:2009 standard and are designated according to the filter type used and have the prefix FF. The devices must have both inhalation and exhalation valves. Examples of gas/vapour and combined filters are: FFA1, FFB2P3, FFK1P2. There are also two types of these respirators i.e. intended to be used for a maximum of a single shift (marked with the letters NR – not reusable), and intended to be used for more than a single shift (marked with the letter R – reusable).
Filters either entirely or substantially consist of filter material. There are particle filters, gas filters and combined filters.
The particle filters should conform to the EN 149:2001 standard and are classified as P1, P2 and P3 in order of increasing filtration efficiency. There are two types of these respirators i.e. intended to be used for a maximum of a single shift (marked with the letters NR – not reusable), and intended to be used for more than a single shift (marked with the letter R – reusable).
The gas filters should conform to the EN 14387:2004+A1:2008 standard and are classified as:
- A - for use against certain organic gases and vapours with a boiling point > 65 °C as specified by the manufacturer,
- B - for use against certain inorganic gases and vapours as specified by the manufacturer.,
- E - for use against sulphur dioxide and other acidic gases and vapours as specified by the manufacturer
- K - for use against ammonia and organic ammonia derivatives as specified by the manufacturer,
- AX - for use against certain organic gases and vapours with a boiling point £ 65 °C as specified by the manufacturer. For single use only,
- SX - for use against specific named gases and vapours as specified by the manufacturer.
Multi-type gas filters - filters which are a combination of two or more of the above listed types, excluding SX, and which meet the requirements of each type separately.
Combined filters - gas or multi-type gas filters incorporating a particle filter according to EN 143:2001.
Special filters are:
- Type NOP3 - for use against nitrogen oxides, e.g. NO, NO2, NOX.
- Type HgP3- for use against mercury.
There are 3 classes of gas filters for types A, B, E and K that are classified in terms of capacity as follows:
- Class 1- low capacity filters;
- Class 2 - medium capacity filters;
- Class 3 - high capacity filters.
The protection provided by a class 2 or class 3 filter includes protection provided by the corresponding filter of lower class or classes.
The classification of combined filter(s) includes that of particle filter(s) according to EN 143:2000.
Type AX and type SX gas filters and special filters are not classified.
There are also valved filtering half masks to protect against gases or vapours and particles. These devices are “disposable” respirators essentially for use against gases and vapours, but with optional protection against particles. Any gas/vapour filters form an inseparable part of the device; any particle filters maybe integral or separable. Complete devices should conform with the EN 405:2001+A1:2009 standard and are designated according to the filter type used and have the prefix FF. The devices must have both inhalation and exhalation valves. Examples of gas/vapour and combined filters are: FFA1, FFB2P3, FFK1P2. There are also two types of these respirators i.e. intended to be used for a maximum of a single shift (marked with the letters NR – not reusable), and intended to be used for more than a single shift (marked with the letter R – reusable).
Facepieces
Half masks: usually reusable moulded face pieces, of rubber or plastic, covers the nose and mouth of the wearer and is held in place with adjustable straps. Air passes through the relevant filter(s) by the wearer’s lung force, or may be supplied by a powered unit or suitable breathing apparatus attached to the mask. The exhaled air passes through an exhalation valve(s). Filters are available for particulates, gases or vapours or as a combination. The mask should conform to the EN 140:1998 standard.
Full-face masks: reusable devices which cover the eyes, nose, mouth and chin, and seals against the face of the wearer. It is held in place (on the head) with adjustable straps. Air is drawn into the mask either through a relevant filter(s) by the wearer’s lung force, or may be supplied by a powered unit or suitable breathing apparatus attached to the mask. The exhaled air passes through an exhalation valve(s). Most masks have an inner half mask. Some devices may be equipped with a speech diaphragm to improve the quality and clarity of voice communication. The visor provides protection against particulates and gases. There are 3 classes of masks: - Class 1 – light duty design intended for use with a filter(s) and light duty compressed airline breathing apparatus, - Class 2 – more robust and offers greater resistance to flammability - Class 3 – for protection against flame and radiant heat. This type is suitable for fire fighting. The mask should conform to the EN 136:1998 standard.
Isolating Apparatus
Compressed airline breathing apparatus are intended to be used in heavily industrial applications. The devices rely on a source of clean breathable compressed air at a maximum pressure of 10 bar. Sufficient volume should be available at the source to supply all the devices connected when working at their maximum demand. Some air supply systems also supply air tools such as spray guns. Their consumption should also be taken into account. The air is supplied to the wearer via a tube(s). This tube(s) can be heavy-duty and have good kink and crush resistance with a length determined by the manufacturer. The light-duty construction is used where there is a low risk of damaging the tube in the workplace. When the compressed air reaches the wearer, there is a basic subdivision of types of equipment which depends on how the air is used. Constant flow equipment – the usual arrangement for this type of equipment is to connect the compressed air supply tube to a belt-mounted flow control valve or regulator. This supplies air at a constant flow to the face piece via a breathing hose. Face mask (half masks, full face masks) visors and hoods can all be used with constant flow devices, but only as specified by the manufacturer.
In the demand valve equipment the compressed air is supplied to a demand valve mounted on the mask. This opens as the wearer breathes in, and closes when breathing out. Demand valves can deliver, with certain limits, enough air for a wearer. The valves come in two versions: - Negative demand – this operates as the wearer’s breathing makes the pressure in the mask fall below that outside - Positive demand – where the face mask stays at a pressure slightly above normal. Both types of demand-type compressed air equipment are normally used with a full-face mask, but it is possible to use half masks. The relevant standards for compressed air devices are EN (to be completed).
Self-contained breathing apparatus consist of a full-face mask fitted with a demand valve and supplied with clean air from vessels of compressed breathable air. Both negative and positive demand types are available. These devices are the most complex, requiring a high degree of training for both wearing and maintenance. The devices are only likely to be used in potentially very dangerous situations. Duration of use is dependent on the size and number of compressed air vessels. Open-circuit compressed-air devices (exhaled air is discharged to the atmosphere) typically lasts about 60 minutes, and is widely used by industry and emergency staff. Closed-circuit compressed-oxygen devices (carbon dioxide in the exhaled air is removed by an adsorbent and the cleaned air is topped up with oxygen and recirculated) can last for more than two hours. The relevant standards for these types of devices are (to be completed)
Self-contained breathing apparatuses for escape purposes are available in compressed-air, compressed oxygen and chemical oxygen types and are intended to be used for a short-duration in case of an emergency escape from hazardous areas. Escape devices should be used for escape purposes only, and should not be used for normal working or entry to hazardous areas.
Selection
Prior to selecting an RPE, it is recommended to identify all types of hazards occurring at a workplace and evaluate the occupational risk (Occupational safety and health risk assessment methodologies). Where appropriate, it is necessary to take the measurement of harmful and dangerous substance concentration and compare the results with exposure limits (Occupational Exposure Limits with respect to concentration, for example, of dust, fumes, gases). Times exceeding the acceptable values will be an indicator as for the selection of protection class and knowledge concerning these factors will point to the necessary range of protection. If the highest acceptable concentration has not been established, acceptable concentration value ought to be established on the basis of e.g. literature data or experts’ opinion. Important information on the subject may be found on the label provided on the packaging of chemical preparations. Moreover, producers, distributors or importers placing a hazardous detergent on the market are obliged to provide material safety data sheets (MSDS) of the substance.
If the risk is evaluated as high and applied collective measures are not sufficient or if conditions do not allow for other alternative protective measures, in order to ensure the safety of a worker, appropriate RPEs ought to be applied. In the case of exposing the workers to carcinogenic substances, the risk is to be evaluated as high. Since carcinogenic substances are included in the group on no-threshold substances, applying individual protection devices may be treated solely as temporary because it does not ensure total elimination of carcinogenic factors, but only lowers its concentration.

Fit Test Requirements
For proper selection of respiratory devices, the term “protection factor” has been introduced which implies face fitting of respiratory face pieces. The factor is associated with the degree of protection that a given respirator (mainly face piece) is expected to provide. The protection factor is connected with a face fit test. There are two types of face fit tests - quantitative and qualitative:
- Quantitative testing is performed using particle counting monitors or controlled negative pressure devices. From the direct numerical measurement, a calculation of the effectiveness of fit - known as a “Fit Factor” - can be determined,
- Qualitative testing is a method based on the tasting or smelling of a bitter, sweet or odorous compound. The method strictly depends on the face piece wearer being able to detect the test compound.
The so-called” tight fitting” RPE should not be used by people whose beard, sideburns or scars, etc. make it impossible to adjust the facial part correctly or they would hinder with proper functioning of the breathing valves. Each time, prior to every use of an RPE, the following ought to be checked:
- whether the RPE is not damaged,
- whether the respiratory valves are not damaged,
- whether the head tapes allow for tight fitting,
- whether the particle filters, gas/vapour filters, multi-gas filters are in good condition, i.e. individual packaging or casing is not damaged and whether the markings correspond to the identified hazard
- whether the RPE has expired,
- for power-assisted respirators, it is also necessary to check: battery chargé and – according to the producer’s instruction – whether minimum volume concentration of air flow is achieved.
After putting on and adjusting the face pieces, it is necessary to check its tightness. In order to do so, the following ought to be done:
- inlets of filtering elements to be tightly covered by hands,
- inhale,
- facial part is correctly fitted and tight if there is hard resistance while inhaling and the half-mask’s walls come closer to the face,
- inlets of exhale valves to be tightly covered by hands,
- exhale,
- face pieces is correctly fitted and tight if there is hard resistance while inhaling and the half-mask’s walls move away from the face,
- in case of noticing any lack of tightness, the facial part ought to be adjusted again and tightness ought to be checked again,
- in case there is no possibility of obtaining appropriate tightness, the face pieces ought to be exchanged.
Training of the RPE
In order to provide the required level of protection, relevant training on how to adequately select, fit, use, maintain and store the RPE is necessary. Training for the employees (RPE wearers) should be tailored to the specific RPE intended for use, and to the application to which it will be put. The relevant training should cover both the theory and practice of various types of RPEs to be used, and it will have to be based on the recommendations and instructions supplied by the manufacturer. The content of the training depends on the complexity and performance delivered by the equipment, and on the target work environment in which the equipment will be used. A typical training procedure/programme shall include:
- introduction to hazardous or harmful factors occurring in the working environment
- explanation of why a specific RPE(s) is needed – applying for the work activities and when to use it as well as pointing out the consequences of not doing so,
- explanation of the basic rules related to how it works (what it can and cannot do),
- explanation of how to select the proper RPE (if more than one type is available),
- selection of the optimum or best type of suitable RPE,
- practice in putting on, wearing and taking off,
- for equipment including a face mask, instruction in achieving the required fitting to the face of the user (fit-checking),
- explanation related to factors which can affect the protection level provided by the equipment,
- pre-use inspection and check of performance, when appropriate,
- practice and instruction in simple user maintenance,
- cleaning and inspection after use,
- correct storage.
Both workers and their supervisors should be aware of the following:
- what are the protective features of the applied RPE,
- what are the consequences of not using it,
- how to appropriately use the RPE according to the producer’s instruction (it should be ensured that the instructions be accessible and clearly written for the workers),
- that the RPE is the last element securing a worker (after all other preventive measures have been taken) and therefore it is vital to apply them throughout the entire time of exposure to a hazard,
- how to clean and when to withdraw the RPE from use.
Trainings concerning RPE use ought to be organized at the employer’s expense and during working hours. Moreover, they should include new or changing types of hazards and be repeated periodically.
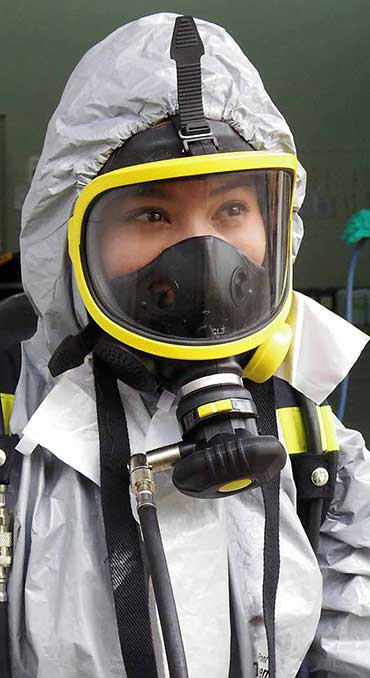
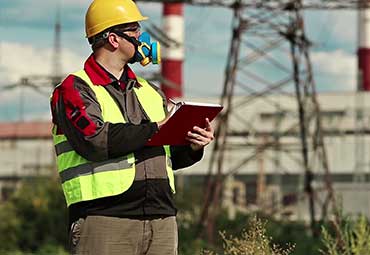
Maintenance of the RPE
An RPE is basically designed for personal use. If circumstances arise requiring it to be used by more than one person, appropriate measures should be taken so as to ensure health or hygiene for the different users. The employer is obliged to ensure washing, maintenance, repair or decontaminating of the RPE free of charge.
Effective maintenance of the RPE is required in order to ensure that the equipment continues to provide the degree of protection for which it was designed. Maintenance includes cleaning, disinfection, examination, repair, testing, and safe storage. Maintenance details are usually provided by the manufacturer. The RPE should be examined before each use, with particular attention being paid to all rubber parts such as face pieces, exhalation valves, breathing tubes, and head harnesses. If the equipment is in a bad condition, it should not be used.
Reusable RPEs require cleaning and disinfection after each use according to the procedures and means specified by the manufacturer.
The user of an RPE may carry out simple maintenance, such as replacing the filter(s), but more complicated repairs should only be undertaken by relevant personnel or service authorized by the manufacturer.
Proprietary spare parts and/or subassemblies need to be used in maintaining the RPE. The use of non-original parts may invalidate approvals and can compromise the health and safety of the wearer.
The RPE should not be stored together with toxic substances or substances that may negatively influence materials from which it is produced, or such materials that give off unpleasant smells.
It is unacceptable that the RPE and its elements be stored in places that may be directly exposed to sunlight or less than 1m from heating devices. The RPE should be transported in conditions ensuring protection from damage and atmospheric influences. Time of storing should be no longer than the one specified by the producer as using expired or damaged filter or gas-filters, and also face pieces, may be the reason of poisoning. In case of reusable filters, directly after leaving the contaminated area, it is necessary to secure it by placing the RPE in an individual airtight container.
After each use, face pieces that are reusable ought to be washed in warm water with soap then thoroughly dried by leaving it to dry in a non-contaminated area. It is recommended to carry out frequent disinfections of face pieces (according to the producer’s instruction) and after each change of user. During periodical RPE reviews and before and after each use, it is necessary to check the correct functioning of valves, and – if necessary – replace the valve. Valves that are out-of-order and lack of tightness may become the reason of very serious poisoning.